Correct propeller size and pitch offer smooth and economical progress under engine. Peter Hawkins explains how he calculated the best combination for his boat
Our Macwester 27, Zena had her engine replaced. Although she was originally fitted with a much smaller engine, it had been replaced at some point with a Volvo MD2B, writes Peter Hawkins.
This had been reworked in 1996 but poorly maintained before our ownership. It breathed its last in dramatic style just as we approached the slipway for our annual haul-out!
In considering a change, we had a choice between 16hp and 20hp engines from Beta Marine.
The old Volvo was nominally a 23hp engine, so a conservative approach suggested sticking at 20hp – which was technically more than needed.
The essence of the tale comes with the fitting and running of the engine.
The hull shape and engine location mean that 15.5° of down angle is required for the shaft. This is partly accommodated by the additional cost of a down-angle gearbox.
The remainder of this down angle is managed by the engine incline, which is then within limits.
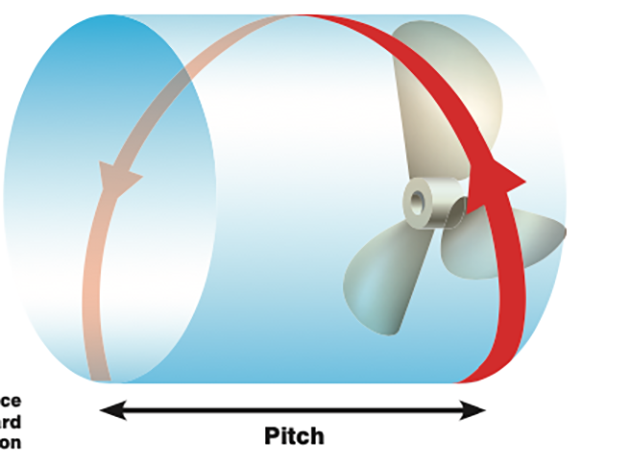
Pitch is the theoretical distance a propeller can ‘screw’ forward in one complete revolution
Due to the angle requirement, there was a limited choice in gearbox ratios: the paperwork we had quoted the ratio as 2.45:1.
Everything for the engine was new. This meant hours (and pounds) for engine beds, complete fuel lines, fuel filter, water inlet/seacock, strainer, hoses, anti-syphon on the exhaust injection of cooling water, full exhaust (including transom fitting, swan neck and silencer), stern gland and stern tube, plus all electrics.
With this in mind, we thought that everything would be fine. The boat propeller was designed for us and given as three-blade, 13in diameter x 12in pitch.
The early sea trials, conducted by Jacky and myself, showed that wide open throttle (WOT) could be just about achieved for the maximum engine revs of
3,600rpm.
This gave a recorded speed of about 6.2 knots (max registered 6.7 knots).
Three weeks later, with three people on board, the engine reached 3,500-3,600rpm.
This should be considered a success by most prop calculation methods. However, not all was well.
Under modest conditions, and at around 2,200rpm, Zena made 3.0-3.2 knots, leaving telltale soot on the transom.
The black smoke is very hard to see, but it swirls around the waterline at the stern.
In a headwind of Force 3-5, the boat noticeably slowed, and it became more difficult to maintain speed.
Winding up the revs would restore some speed, but this was highly dubious and increased the smoke. What was wrong?
‘Over-propped’ is the classic answer, but why and how? The answer to this question has taken some considerable thinking and research.
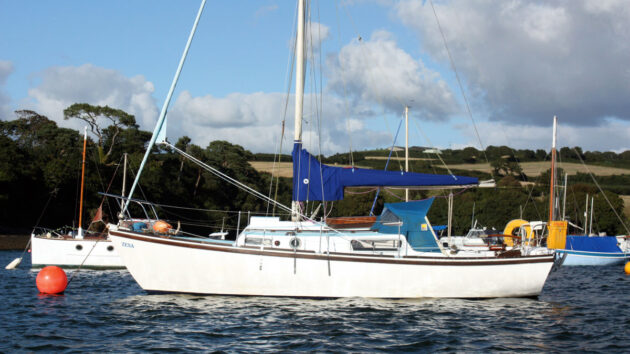
Peter and Jacky Hawkins replaced the engine in their Macwester 27, Zena– and then the propeller. Credit: Peter Hawkins
Engine revs at 3,600 with a 2.45:1 gearbox gives 1,469 shaft rpm (engine revs/gearbox ratio). Shaft revs multiplied by pitch (12in as given) gives 17,632in per minute.
Converting inches per minute into knots requires a division by 1,215, which gives 14.51 knots.
This final figure does not consider propeller slip.
On ‘slow’- moving displacement yachts, this figure is often targeted at 50%. This equates to 7.25 knots (14.51 x 50%).
Our Macwester is 23ft on the waterline, has bilge keels and a skeg forward of the prop and rudder – quite a cluttered profile under the water.
The prop shaft’s angle adds to the complications and a propensity to ‘squat’ stern down.
Having crew in the cockpit only adds to stern-down trim, although this is barely noticeable at lesser speeds/engine load.
The formula for hull speed is quoted as 1.3 knots, or as much as 1.5 in some cases, times the square root of waterline length (feet).
For Zena, this equates to between 6.2 knots and 7.2 knots, of which the lower figure seems more plausible.
Herein lies the problem with the method and the propeller. The hull speed is not a fixed number but an indication.
The fact is that even if you had 100hp, the boat will only go marginally faster as it attempts to push an ever bigger bow wave of water out of the way.
Propeller pitch: Balancing act
The engine and propeller combination act in a balancing manner.
The engine is fuelled by design to achieve so many rpm, but the actual rpm achieved is balanced by the mechanical load created by the propeller in the water.
The WOT test merely looks at whether the engine will attain a loaded rpm. It does not account for the variation in values of hull speed.
The actual maximum engine revs are also an area of variation.
There is an engine speed at which damage can occur. Less than this speed is a region of decreasing efficiency, lower torque, and eventually reduced power despite the higher revs.
Trying to determine a variance on this limit is difficult, but easily reaches 10%. The net result is a prop which is non-optimal.
Another approach is to take the more ‘knowable’ figures and calculate backwards.
In Zena’s case, the hull speed is taken as the conservative 6.2 knots. The engine revs are taken as the nominal maximum of 3,600rpm.
The hull speed of 6.2 knots divided by 50% (prop slip) gives 12.4 knots theoretical screw speed. The screw speed of 12.4 knots x 1,215 (convert to inches per minute) = 15,066 inches per minute: 15,066 divided by 1,469 (shaft speed) = 10.25in.
All these calculations are affected by that major variable, prop slip.
Prop slip is 100% when you are tied to the dock with the engine running in gear.
All that happens is that you move a volume of water and add strain forces to the mooring lines.
While under way, the prop slip is a function of all the hull dynamics, the load (including crew) and any headwind or sea. At higher loads, the prop will slip more.
A smaller prop?
When we asked about changing the propeller pitch to 10in, there were questions as to why we wanted to do that.
There were also doubts about the gearbox ratio. Eventually, I ended up placing white tape at 12 o’clock on the engine crank pulley and the tip of a propeller blade.
I then turned the prop by hand in gear and observed the rotation. A half-turn of the screw gave one turn of the engine.
We had a 2:1 gearbox, not 2.45:1! I was told that 2:1 was the figure used in the original propeller calculation, but I’m not sure if this is correct or not.
Taking the WOT figures, poor Zena was trying to achieve 8.88 knots (17.77 x 50%) with a 12in pitch prop. It’s no wonder there was black smoke! So we changed to a 10in pitch prop.
Of course, with a smaller prop it would be possible to over-rev the engine, but this is no different from the majority of cars, and most of us can be trusted not to over-rev them in daily use.
Same revs, more speed
Only 25 engine hours were logged in the first season: the engine hours increased in 2012 and 2013.
At the outset, 2,200rpm with a 12in prop generated 3.2 knots. Recordings in 2012 with the 10in prop showed 4.0-4.2 knots at 2,500-2,600rpm.
At the end of 2012, the stern gland was adjusted. By 2013, 4.4 knots @ 2,400rpm and ~4.0 knots @ 2,000rpm were recorded. This latter discrepancy could partly be a function of running in.
The slip calculations suggest she is still marginally over-propped, but it does depend on what you call the hull speed.
Some people use 1.5 (not 1.3) times the square root of hull length to define the limiting hull speed.
Beta Marine also suggests a prop that is up to 7% overload of torque.
However, the reality is that Zena is far more resilient in headwind or sea – a bonus which is hard to quantify but easy to experience.
The fact that we are now achieving better speed for lower engine revs underlines another misconception: it is considered that reducing propeller pitch is like slowing a boat down.
On paper, 12in for one turn of the propeller screw is more progress than 10in.
But in the world of boats, it’s not that simple. ‘Efficiency’ is what it’s all about.
Optimum progress through the water is made when the engine/fuelling is balanced with the load (torque) on the shaft. The load is the boat being pushed through the water (and wind + dinghy drag, if towing).
To avoid confusion, propeller slip is not a byword for efficiency.
With 0% slip, there would be no forward thrust or driving power. With 100% slip, there could be plenty of driving power but no forward motion (ie when the boat is tied to the quayside).
The desired slip is all in the balance of things, and as already mentioned, the rule of thumb for displacement yachts is prop slip of 50%.
Fuel consumption and speed are also worth noting when determining propeller pitch. An overloaded/over-propped engine will not develop enough torque to turn the shaft as quickly as it should.
The shaft slows down, and the fuel is burnt with less air, which results in unburnt fuel (soot) being emitted.
An under-loaded engine will happily buzz around, but it is not giving as much output for all the fuel it is burning.
When matched, you have the right power out (boat movement) for the fuel/air mix input, and this means smooth engine running and economical motoring.
Perhaps this revised method of calculation will help to keep a check on propeller pitch, whether you are buying new or running what you already have.
Boat propeller: How to choose the right one for your boat
The correct prop can have a dramatic effect on your boat's performance. Ali Wood learns how you can save fuel,…
Fouled propeller fix: top tips for solving the problem at sea
What should you do when you catch a line or fishing net and your prop becomes fouled? Ali Wood looks…
How to fit a folding propeller
Mark Ryan shares how he removed the old propeller on his Albin Ballad and replaced it with a two-bladed Flexofold…
What causes a propeller to go pinkish in colour?
While Rod Stuart was scrubbing his boat, he saw the anode had fallen off and his propeller was turning a…
Want to read more articles like How I achieved optimal propeller pitch?
A subscription to Practical Boat Owner magazine costs around 40% less than the cover price.
Print and digital editions are available through Magazines Direct – where you can also find the latest deals.
PBO is packed with information to help you get the most from boat ownership – whether sail or power.
-
-
-
- Take your DIY skills to the next level with trusted advice on boat maintenance and repairs
- Impartial, in-depth gear reviews
- Practical cruising tips for making the most of your time afloat
-
-
Follow us on Facebook, Instagram, TikTok and Twitter